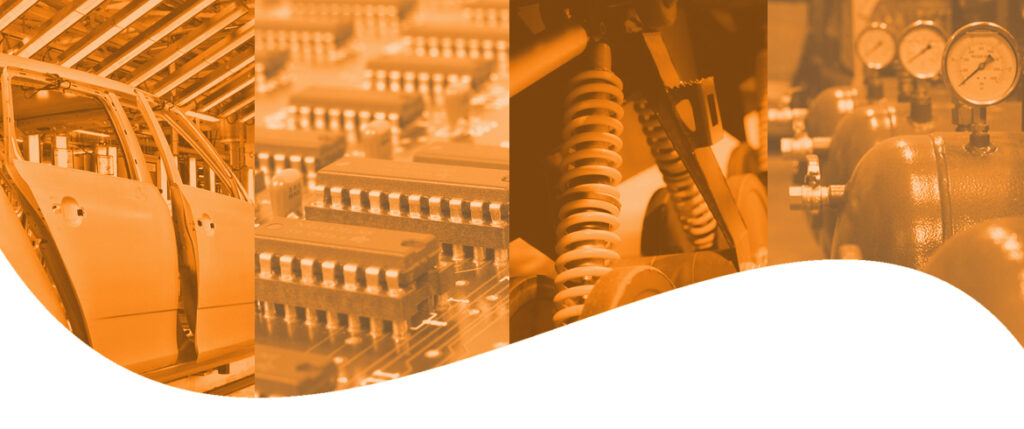
Welding for Every Application
Artech’s CD Projection and Stud Welding machines are used across a wide range of industries and applications. Starting from some of the world’s largest companies to small and medium enterprises, Artech’s technology is trusted equally by all.
In several of the industries below, Artech has pioneered and successfully led the shift from conventional welding to Capacitor Discharge welding, to deliver better quality and productivity.
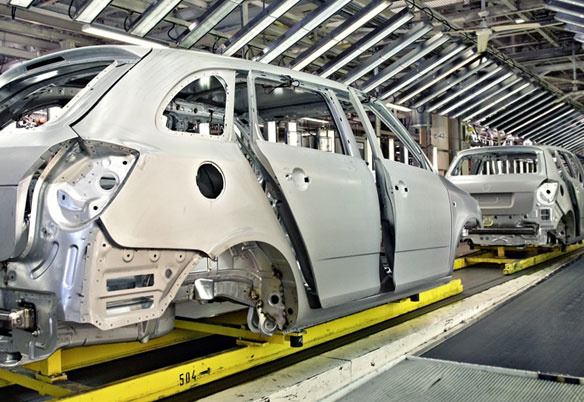
Automobile
Semiconductors
Artech understands the special welding needs of semiconductor industry. With strong, leak proof welds and excellent aesthetics, Capacitor Discharge welding has led to greater adaption of Artech’s machines in semiconductor applications. A majority of Artech’s CD Projection and stud welding machines are used in thyristor manufacturing process.
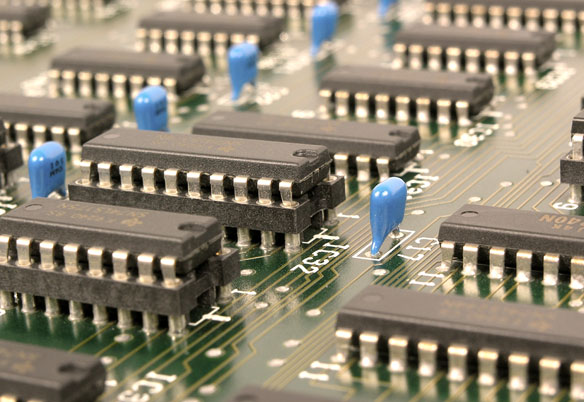
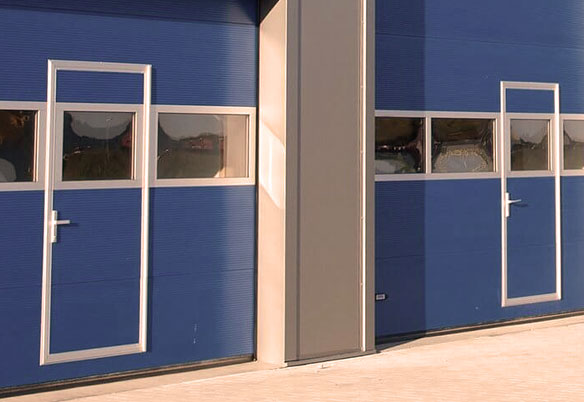
Metal Doors
Compressor Parts
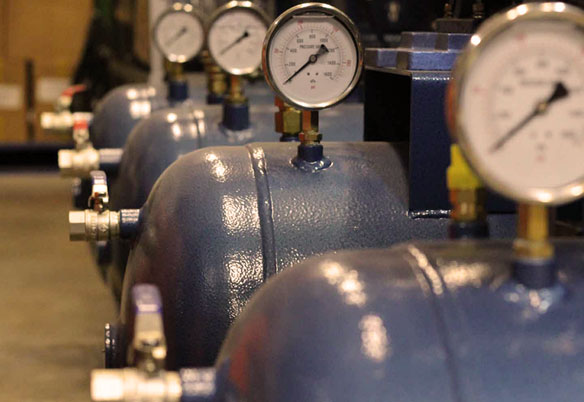
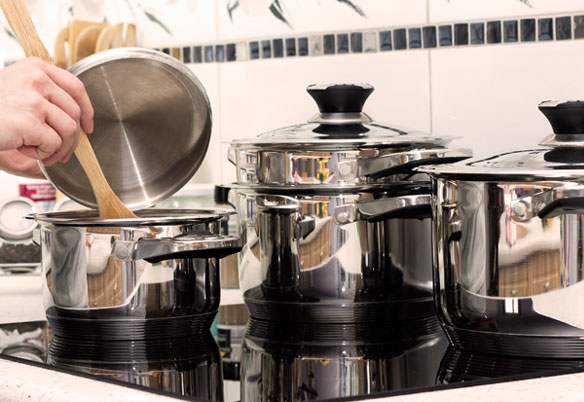
Kithchenware
Diamond Segment Welding
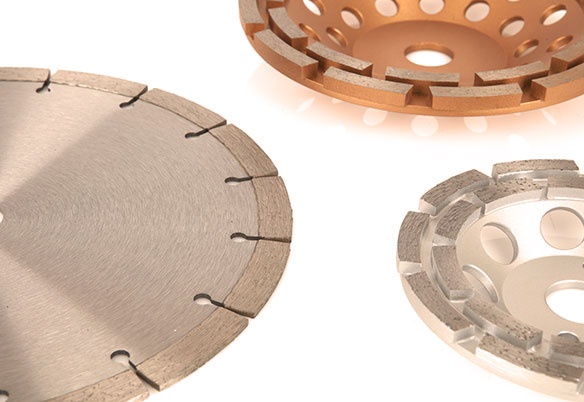
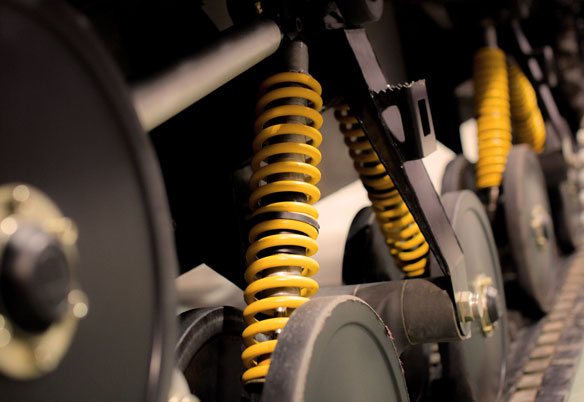
Leak Proof Welds
Pump Impellers
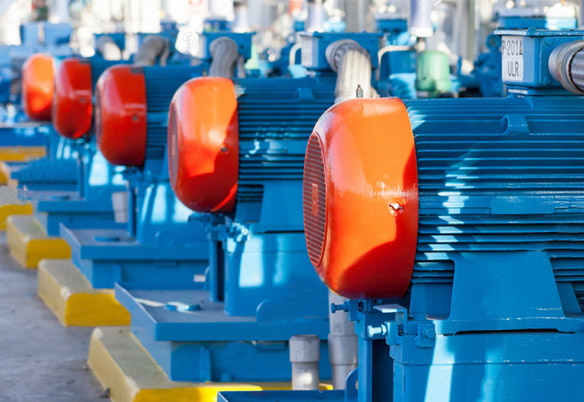
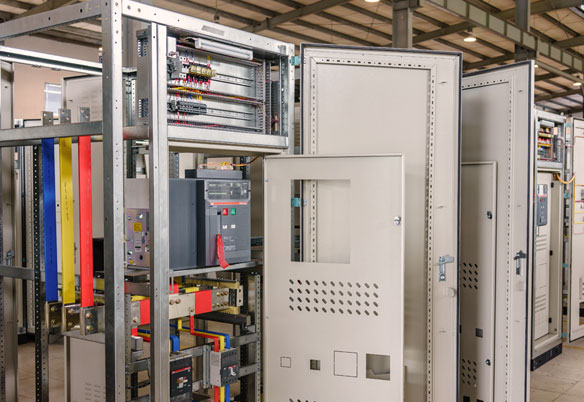
Control Panels
Need help to shift to better welding?
- Free trials to prove your welded components
- Select the best Machine design & related automation
- Test and prove the welded component